This is the part that will keep the rain that runs in along the door edge off of me. This will fix one of the only criticisms I have come across of the Milan. There are still the usual ones of cost and weight but they also apply to all other velomobiles.
The flange the door closes on slants inward so any water getting to it will run inside the velo. The above part has three purposes: the first to direct water into the bottom of the velomobile, the second to round off the otherwise sharp edge of the door lip and the third to stiffen up the door edge. One could make the edge thicker but this will add more weight than the above part. The other choice would be to use a soft gasket the door closes down onto. For my experience with gaskets in kayaks, this was not the way I wanted to go. Besides, the finished look of the Milan is nicer without the gasket sticking out. There is a small gap between the front of the hood and the door just above my shoulder. This lets most of the rain in. Now with the gutter it can no longer drip down onto me.
The rain gutter is two layers of carbon fibre with a third layer on the inside edge. Weight of the part is less than 50 grams. If you cost it out based on weight and the time it takes to make it, it might be one of the most expensive bits in the Milan. At first I thought I could get away with a contact laminated part, but it needs to be vaccuum bagged as the material doesn't always stay in the sharp contours.
Thursday, December 20, 2012
Wednesday, December 12, 2012
Milan Handle
The retracting hand hold on the back of the Milan is easy to install. Installation on other velomobiles would be similiar.
Here you can see the two holes drilled in the back of the shell. I first drill a small hole with a 3/16" bit, follow this up with a countersink to carefully bevel the gel coat slightly wider than the finished hole. The reason to bevel the hole is to prevent chipping of the gel coat when drilling the final sized hole. Then I drill the hole to the final size, in this case 1/4".
What it looks like on the inisde. I glassed on the anchor point but you could also bolt the "p" clip in place. There is a 30" piece of 5 mm rope and a 22" piece of shock cord. The reason for this much lenght is so you can reach it after the rear fender is in place and replace the cord and shock cord if necessary. The top of the Milan is permanently bonded to the bottom so there is limited access. Reaching around the fender is difficult as I discovered putting the first handle on the first Milan GT.
Here you can see the two holes drilled in the back of the shell. I first drill a small hole with a 3/16" bit, follow this up with a countersink to carefully bevel the gel coat slightly wider than the finished hole. The reason to bevel the hole is to prevent chipping of the gel coat when drilling the final sized hole. Then I drill the hole to the final size, in this case 1/4".
What it looks like on the inisde. I glassed on the anchor point but you could also bolt the "p" clip in place. There is a 30" piece of 5 mm rope and a 22" piece of shock cord. The reason for this much lenght is so you can reach it after the rear fender is in place and replace the cord and shock cord if necessary. The top of the Milan is permanently bonded to the bottom so there is limited access. Reaching around the fender is difficult as I discovered putting the first handle on the first Milan GT.
The finished result with the rope pulled snugly against the back of the shell. The distance between the holes is 8.5cm. The previous one was a bit longer but I like the new lenght better.
Thursday, December 6, 2012
Heat and hold down jigs
Now that the heating season is here I have had a pellet stove put in the shop. So far I am quite pleased with its performance. One does notice how much fuel it uses as you need to fill it manually. The big advantage over just a wood stove is that to light it you only press a button. It also burns very cleanly as you do not see smoke coming out of the chimney only some shimmering from the hot combustion air going out. My other choice here for heat other than wood is to use electricity. The vast majority of the electricity used in BC comes from hydro power but some is from coal fired power plants in Alberta and some from burning natural gas. Using electricity is much more expensive and not the greatest choice for being carbon neutral. I do have some baseboard electric heaters as backup heat. They will be used a bit when I have specific areas that need more heat. Luckily, for the most part, I only need the extra heat for short periods.
A side benefit of having bags of pellets is that I have found another use for them. Some of the moulds are odd shapes and hard to hold in place when you are working on them. Partial bags of pellets make good weights to hold them in place. Here is an example of a couple in use.
Wednesday, December 5, 2012
Weight
Here I am weighing the left side bottom part to see how much lighter the carbon/Kevlar part is than the glass part. This part ended up weighing 2300g with a saving of 1160g. There is still some potential for a bit less weight maybe 100-200g but that would have to be done carefully after seeing how this laminate works out. The other two shell parts were a bit lighter with all three weighing in at 6.7 kg (14.74 lbs).
I have made the other major parts and the total weight saving is going to end up around 4 kg. This will mean a finished weight of around 26-27 kg(57-59lbs) when equiped with 70 mm drum brakes and the lighter rims and tires.
Monday, November 26, 2012
Progress on the next Milan
The first seat and carbon wheel well.
The carbon wheel well came out quite well. There is a reasonable weight saving from the glass/Kevlar version. This part takes me a long time do as all the material needs to be glued in place before I put the bag on. Being a fairly complex shape the carbon is in relatively small pieces which each need to be handled separtely. The bag ends up with lots of wrinlkes in it which makes finding and fixing a leak a real challenge. This of all the parts for the Milan is the one we will have the highest failure rate with. I would much rather make a top or side of the shell as they seem to go quicker. The shell parts do actually take quite a bit longer and I like to have two people when we wet out the part. Much more satisfying when you demould a large part.
I am making up all the small parts for the next Milan so I can assemble the next one without being held up waiting for these parts. This is also a good way to check that all the moulds are ready to use. I anticipate that the first Milan GT for sale will be built in January.
Sunday, November 18, 2012
Two Hoods
This is the new larger hood I can comfortably wear a helmet in.
What it looks like from behind. I have some thin foam attached with Velro to the back edge of the hood to add a bit of ventilation. They are removeable so I can experiment with what works best.
Close up of the slots that control the shape and position of the visor. To open it you just push it up with your finger. It stays in place quite nicely at whatever position it is set at. To close it I have a short cord attached at the bottom edge that hangs down inside. Just pull the cord toward you and that side closes. Pull the other side and it is closed. The cords are still a bit of a work in process. Maybe a small hole in the middle of the visor at the bottom edge so you just use your finger to close the visor. The other idea is a lexan loop bolted on the bottom edge instead of the hole. The hole even if it is small will let a fair bit on water in at speed.
The two hoods in an end on view. the original hod is on the left. The new Milan GT XL hood is on the right.
Wednesday, November 14, 2012
New Hood
I have decided to build a slightly larger hood so I can comfortably wear a helmet while riding. Here in this part of Canada riding with a helmet is a legal requirement. I have been riding with a helmet for a long time now and it just doesn't feel right without. The other consideration is that if you were involved in a serious accident the insurance award can be reduced by estimated protection the helmet might have provided.
I ended up making two different front visors as the shape of the new hood is a bit different. The original is the top one in the photo. It seemed to take forever to get the right shape as I had to make the first one by hand and then transfer it into a CAD program. I then used that to create the file for my CNC router. A couple of revisions later and we have visors. The advantage of cutting them on the CNC router is that they will all be the same so replacement is straight forward. Besides, making the slots freehand was no fun.
Wednesday, November 7, 2012
Mirror Fairing and Hood
The first mirror fairing. It turned out rather well but I orignally had the a bit too far back. You can see the first mounting hole closed off by a bolt.
The reason for moving was that when using the hood the foward bolt holding the windshield was covering part of the mirror.
When I came back from the first ride in the rain I sat in the velo for about ten minutes just enjoying being dry while it rained away outside. When necessary I could pop the windshield open to see under it. Once over about 25 kph I rode with it closed but going up hills slowly I had to open it as my breath fogged it up.
Monday, October 29, 2012
New chain covers and another ride
The other half of the cover, this one covers the front of rear derailleur and prevents stuff from getting caught in the chain. I already had my repair bag slide back inside the velo and had to stop to move it. This should also make loading gear much easier as it will no longer be able to interfer with the mechanical bits.
I have had a couple more rides in the Milan. It feels like it has lots more potential to really zoom along. Still quite a few details to finish up. I am presently working on the seat moulds, small mouldings for the mirrors and signal lights. Now that I an almost finished I can see that it will be very nice once its all done.
Just before leaving the community centre I saw a couple of cyclists ride by heading the direction I was planning on going. As I got going a couple minutes later I was not expecting to see them again. It is mostly downhill for the first while and I got up lots of speed, enough that I thought about braking. A bit of up and then some more down followed by some corners and then an uphill section where I end up in the lowest gear. As I came around the last corner the two cyclists were just in front of me. We all rode up the hill together and chated some. At the crest of the hill they pedalled away to pick up some speed for the downhill. I just coasted and was soon overtaking them, then they faded from sight behind me. There is no point in pedalling to pick up speed at the top of this hill as it has a couple of corners where I need to brake. Maybe as I get more used to the Milan I can just let it run but I doubt it as the road is not banked enough. I stopped for coffee and before getting coffee there was a some crowd gathered around the velomobile. One fellow talked over and remarked somewhat touch in cheek "what are we all doing standing around looking at the Harley". The two cyclists I passed were there taking a closer look and we all just all grinned.
Tuesday, October 23, 2012
Interior Pictues
One thing to note on the interior is that I have not painted the inside black. I like being able to see into the laminate when vacuum bagging the parts. The primary reason for painting the inside black is to hide the dirt that gets caught in the nooks and crannies of a hand laminate. The other one is to hide any tiny bubbles in the laminate. The interior surface from the wheel wells back is quite smooth from the bag. From the back of the wheel wells foward I used some peel ply to simplify bonding and deal with the bag lines due to the complex shape. I have noticed that this area does stay as clean looking.
View of the other side. One small modification I am making is to change the rib at the back where the rear suspension bolts on. It just fits now but a bit more space so it can't rub when the swing arm moves is a good thing.
The view forward. Reverse gear is with your left foot. Before I always used my right foot but the adjustment was not difficult. Note the wires hanging down for the brake light from the right brake lever. I haven't added the signal/brake lights yet.
Friday, October 19, 2012
Second Ride in Milan GT
Second ride in the Milan was to the store and back. Fastest round trip yet. It was about two minutes faster than the Borealis. Most the the gain was in carrying more speed up the next hill. There is one short steep section of downhill before the first real uphill going to the store. I was able to crest the hill in the big chainring. The only problem with this section is that just before you reach the bottom of the hill there is a road coming in from the right. Just a little way up from this road on the hill there is a dip which hides you from drives turning onto the road. I am careful turning onto the road even in the car as it is hard to be sure no one is coming. I am cautious in the velomobile approaching this intersection as the velo is lower and even harder see than a car. If that intersection was more visible I could probably gain 10 kph. The way it is now I can only go for after the road which only leaves a few meters of downhill to gain more speed on. Never the less I did get to 71.2 kph and the Milan felt rock solid. I didn't think I was going that fast but the GPS confirmed the speed. On the way back just a ways before my driveway I was held up a bit by a car turning around. He looked lost as he turned around in my driveway.
Monday, October 8, 2012
First Ride in Milan
I had the first short ride in the Milan GT yesterday. Brock from Cambie Cycles rode up from Vancouver and helped set up the drive train. After this and some lunch, we rode around a bit to compare the Borealis V3 and Milan. Coasting downhill, they are about similiar speeds until you get above 30-35 kph. At this point the Milan is much quicker. I suspect that below 30 kph or so most of the resistance is rolling resistance. Once over 40 kph, the sleeker shape of the Milan comes to the fore. We rode a little further than Brock really wanted to just so I could compare speed up a hill which has a nice downhill section just before it. At the top on the hill I was still in the big ring moving along quite quickly. The extra speed on the downhill compared to the Borealis accounts for the higher speed at the top of the hill. I'll have to ride to the store and back to see how much faster the Milan is. I am a couple minutes quicker on the round trip with the Borealis (around 25 minutes) than with my high racer. If I could save a minute or two this would be lots. After this short comparison ride I rode with Brock back to the ferry. Going up a couple of hills I really noticed that the Milan is very stiff. I couldn't feel any flex so the bit of reinforcing with carbon fiber makes great sense. Now I just need a bit lower gearing for my hills around here. They are pretty short about 6 minutes max but about 7-8% with steeper sections.
Now that I have had the Milan sitting around I have got quite used to the shape. Everytime I look at it I see something different. The nice rounded shapes and bumps are really likeable after you get used to them.
Now that I have it rideable I can mention the weight as it is no longer just a calculation. It now weighs 32.3 kgs with 90mm drums. This is essentially a glass laminate with a small amount of Kevlar and carbon fiber used where it benefits most. Had I used the lighter tires and wheels with 70mm drums the weight would be just under 30kgs. I feel it is still a little bit overbuilt as I overdid it in some spots. In fact to see how stiff it was in front of the door where there is a lot of reinforcement, I was able to stand on it without even any funny noises. It wouldn't have been good to fall off and damage it before I even had a chance to ride it. Standing on your velomobile is not a recommended activity!!
Tuesday, September 18, 2012
Rear Fender First Attempt
Being assembled after bagging the part. The parts have a small flange left on them which I can use for alignment. In the photo you can see and two extra ridges I added for some more stiffness. I stopped the kevlar short of the area you trim out for the rear wheel axle. Kevlar does not trim cleanly as it is almost impossible to sand a smooth edge. Cutting it is not fun either.
The other side with more stiffening ridges. The black shadow arround the ridges is the carbon plate I glueing on the inside. While it accomplished the goal of adding some stiffness, it is way to labour intense to repeat. The next one will have a small strip on foam in the ridge which will do about the same for less weight. After I installed the fender and checked clearances for the rear wheel I spotted another small improvement I want to add. This one should be easy to do. It will creat a bit more space around the spokes on the cassette side. The fit is tight here so gaining even 2mm is a big deal. It should make it simpler avoid any rubbing issue between the spokes and the fender.
The first Milan is now sitting on it's wheels. We are getting closer to the first ride.
Monday, September 10, 2012
First Milan GT Shell
The first shell is now assembled. It has been a long time getting to this point. There is still quite a bit more to do before I can ride it. All the bike bits need to be added. The stripe along the side will be a custom cut reflective vinyl. The lights and turn signals are still missing. The hood and door moulds still need sanding and polishing.
For the first one it has come out really well. I am very pleased with the stiffness and the weight. I did end up using some Kevlar and carbon fiber for reinforcing in selected areas. It is still mostly a glass laminate. For what I can tell it looks like the weight will be closer to what carbon velomobiles weigh than a glass one.
Friday, August 24, 2012
Rib Bonded In
The did a quick hand layup of the rib yesterday using some carbon and basalt. It ended up weighing 178g and should be tough enough to stand on. I couldn't get any deflection by pressing on it in the middle, supporting one end on the bench. I didn't try really hard as this wouldn't be a good test as once its bonded in the shell, the shell will add more stiffness. Another reason I didn't try too hard is that the rib was not even close to fully cured.
I glued the rib in and could check out it's effectiveness today. First I put the part on the floor on some foam and stood on it. Definitely strong enough. Then I supported it on some blocks on either end and stood on the middle and jumped around carefully. My conclusion is that it is a bit overbuilt. It took about 50g to bond in so ultimately with a bit better layup using vaccum, just slightly less material the finished weight bonded in could under 200g. Now just to make at plug and mould so I can do one for the other side. Looking down on it from above.
Wednesday, August 22, 2012
Shell stiffener
Managed to get the part I was worried about out of the mould without it sticking like the last one. The left side bottom section of the shell is an experimental part to test the mould and planned laminate. The test in the laminate is to use some Kevlar as the reinforcing bits instead of glass in a glass part. Kevlar will add some impact resistance and it's lighter than glass, being less dense so it builds thickness with less weight. Kevlar seems to reduce transmission of noise through the shell. If it proves its worth I will use it in the standard glass laminate. Not adding it due to the extra cost would be short sighted provided it works.
After examining the stiffness in the floor I decided that a stiffening rib as the best way to stiffen it up. The other option I considered was adding a foam or honeycomb core. The core is more work and may not be lighter. The stiffening rib would go from the back edge of the wheel housing to where the rear suspension pivot is mounted. The rib along with the very stiff corner at the bottom edge of the shell should act as a frame on either side of the shell. If it works as well as I think it will the drivetrain should be very stiff. This should help with climbing as there will be no losses due to flexing. Here is a picture of the pattern I am developing for the stiffening rib.
Other velos seem to have an aluminium frame member running under the seat (Mango) or an aluminium extrusion running in the chain trough (Quest). Hopefully my solution works better than either of these methods. If the stiffening rib is strong enough to step on beside the seat you will have some options for getting in and out by not being limited with only putting weight on the the bridge between the wheel housings. There will be another rib bonded to the side of the shell from the bottom corner to where the crossmember from the fender ties in with the sides.
After examining the stiffness in the floor I decided that a stiffening rib as the best way to stiffen it up. The other option I considered was adding a foam or honeycomb core. The core is more work and may not be lighter. The stiffening rib would go from the back edge of the wheel housing to where the rear suspension pivot is mounted. The rib along with the very stiff corner at the bottom edge of the shell should act as a frame on either side of the shell. If it works as well as I think it will the drivetrain should be very stiff. This should help with climbing as there will be no losses due to flexing. Here is a picture of the pattern I am developing for the stiffening rib.
Another one with the rear suspension taped about where it mounts.
Other velos seem to have an aluminium frame member running under the seat (Mango) or an aluminium extrusion running in the chain trough (Quest). Hopefully my solution works better than either of these methods. If the stiffening rib is strong enough to step on beside the seat you will have some options for getting in and out by not being limited with only putting weight on the the bridge between the wheel housings. There will be another rib bonded to the side of the shell from the bottom corner to where the crossmember from the fender ties in with the sides.
Monday, August 20, 2012
Stuck
It finally happened. I stuck a part in a new mould. This hasn't happend for a few years and it is always a suprise when it does.
I did manage to get the part out of the mould after a long struggle. You can see where the gel pulled off the part and stuck to the mould. I had to cut and break up the part some to get it free. I was even able to chip the stuck gel off the mould without damaging it. I only have a small bit to sand off. It's only about the size of my thumb nail. Luckily it didn't stick where the suspension strut fastens at the top of the wheel well. There is a bit more to sand around the edge of the mould where the vinyl ester resin really stuck. This was on the flange where there was no gelcoat. Vinyl ester does stick much better than polyester gel coat. It the future I will use PVA in new moulds until they are broken in. I thought lots of coats of wax would do the trick but I guess not.
I have another mould sprayed up which I am hoping will release well. This mould was treated the same as the one I stuck the part in. I am keeping my fingers crossed that it comes out OK.
Monday, August 13, 2012
Surprise, not riding velo much
There is a reason for not riding one of my velomobiles much. I have a high racer that I am trying to get down to under one dollar per kilometer. It has taken quite a while to get to this point where I am close to the goal as I have had the high racer for three or four years. Obviously I have not ridden it much opting to use a velomobile instead. It is a Bacchetta Strada that I bought from Cambie Cycles for a good price. I do have some criteria for doing this, it has to warm enough to ride with short sleeves, it has to be dry, there have to be some hills and the ride can't be too far. Riding to the post office or store on the island fits these conditions but at only 10 km for the round trip you don't knock off very many kilometers.
Last week end I went for a longer ride catching the ferry over to Vancouver Island. It was a nice warm sunny day and I rode too far without eating and drinking enough so the last bit of the ride wasn't as pleasant as it should have been. The last steep hill after getting off the ferry to Quadra Island was tough. Had I been in my velomobile I would most likely have stopped and rested very briefly on the hill or gone at a very slow pace in low gear. On the high racer I don't have the option of stopping without getting off(walking is uncool but can be necessary) and it is geared a bit high to go slow enough. If I rode much slower balance becomes my main issue. I did the same ride just a couple of days ago and felt much better. A bit more liquids and some food did the trick. I did have a good tail wind for the first part of the ride and was holding 38-40 kph which was great except I would have to ride back against it.
I finally rode the velo to the post office the other day. The big surprise was that I was faster than with the high racer. The trip ended up being 25:38 minutes compared to around 28-30 on the high racer. I had assumed that I would be faster on the high racer as it is a bit hilly. The reason the velo was faster is that I could carry a bit more speed from the downhills to the uphill. The hills are fairly short but terrain is not would I would call velomobile friendly. Not enough rolling hills just some short steep bits. Curious to see if the Milan GT will be even quicker as I should have a bit more speed coming into the uphill bits. Even just a few more kph cresting the hills would make a big difference.
Last week end I went for a longer ride catching the ferry over to Vancouver Island. It was a nice warm sunny day and I rode too far without eating and drinking enough so the last bit of the ride wasn't as pleasant as it should have been. The last steep hill after getting off the ferry to Quadra Island was tough. Had I been in my velomobile I would most likely have stopped and rested very briefly on the hill or gone at a very slow pace in low gear. On the high racer I don't have the option of stopping without getting off(walking is uncool but can be necessary) and it is geared a bit high to go slow enough. If I rode much slower balance becomes my main issue. I did the same ride just a couple of days ago and felt much better. A bit more liquids and some food did the trick. I did have a good tail wind for the first part of the ride and was holding 38-40 kph which was great except I would have to ride back against it.
I finally rode the velo to the post office the other day. The big surprise was that I was faster than with the high racer. The trip ended up being 25:38 minutes compared to around 28-30 on the high racer. I had assumed that I would be faster on the high racer as it is a bit hilly. The reason the velo was faster is that I could carry a bit more speed from the downhills to the uphill. The hills are fairly short but terrain is not would I would call velomobile friendly. Not enough rolling hills just some short steep bits. Curious to see if the Milan GT will be even quicker as I should have a bit more speed coming into the uphill bits. Even just a few more kph cresting the hills would make a big difference.
Wednesday, August 8, 2012
Last Mould
I am presently working on the last mould--not really the last mould but the last needed to make the first Milan GT.
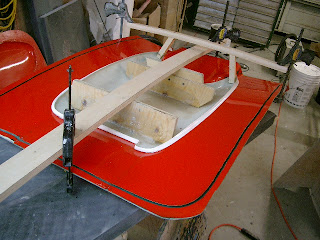
Here you can see a trial fit of the door plug into the mould before making the return flange. I am a bit worried that I may have to redo this mould if it does not fit well enough. Having to press the plug into the mould I made it off of is not a good sign. It may well work just fine but there is no way of telling until I make an actual part and fit it to the shell. Progress has now sped up a bit as I finished the kayaks I had on order. Here is a picture of them and the Milan GT plug. If the Milans come out as nice as these kayaks I would be very pleased.
Here you can see a trial fit of the door plug into the mould before making the return flange. I am a bit worried that I may have to redo this mould if it does not fit well enough. Having to press the plug into the mould I made it off of is not a good sign. It may well work just fine but there is no way of telling until I make an actual part and fit it to the shell. Progress has now sped up a bit as I finished the kayaks I had on order. Here is a picture of them and the Milan GT plug. If the Milans come out as nice as these kayaks I would be very pleased.
I have been walking by the Milan plug a few times every day for a while now. The shape is growing on me. When I first saw it on the internet I was doubtful about liking the shape. This was until I saw it in person during ROAM. It really does look much better in person than on a flat screen. While some may like a simpler shape, the nice flowing curves remind me a bit of shapes found in classic old sports cars. Depending on how the light hits it, it always looks a bit different. My biggest decision will be what colour to build mine. I am leaning towards the blue that is in the kayaks. My second choice is white as it very visible and dresses up really well with a contrasting coloured stripe. A distant third is a dark green much like British Racing Green. The reason I won't go with the green is that it shows every little scratch. Yellow is out as we build about 40% of our kayaks in it and while I like the colour I see too much of it.
Thursday, July 12, 2012
Three More Moulds to Go!!!
I now have three more moulds to make before I am ready to start on building the first Milan GT.
The one of the left is the storage tray that mounts in front of the left side wheel housing. There isn't one available for the right side but if I find it really useful I will make one for that side too. The down side of this is that you end up with more stuff as once its in there you do tend to forget about it. Both of these storage areas together are about the volume of a mid size pannier. The middle one is the hood. It should be fairly straight forward to make once we have the mould with a flange on it. The right one is the door. It will need to be a two part mould as it has some undercuts. There are three different sizes of door but I am starting with the one with the biggest bumps. The others can follow later. Same applies to the small mouldings used to mount the side stick steering and electrics.
It seems to have taken forever to get to this point. There is still a lot to do before the moulds are ready to use but that is just sanding and polishing. I will be quite happy to see the end of the sanding as its boring to do but you do need to be careful to do it properly. More skill required than you would think at first glance. I can only sand for a while each session as my hands an elbows can only take so much. It's not so bad if you are outside on a sunny day.
The one of the left is the storage tray that mounts in front of the left side wheel housing. There isn't one available for the right side but if I find it really useful I will make one for that side too. The down side of this is that you end up with more stuff as once its in there you do tend to forget about it. Both of these storage areas together are about the volume of a mid size pannier. The middle one is the hood. It should be fairly straight forward to make once we have the mould with a flange on it. The right one is the door. It will need to be a two part mould as it has some undercuts. There are three different sizes of door but I am starting with the one with the biggest bumps. The others can follow later. Same applies to the small mouldings used to mount the side stick steering and electrics.
It seems to have taken forever to get to this point. There is still a lot to do before the moulds are ready to use but that is just sanding and polishing. I will be quite happy to see the end of the sanding as its boring to do but you do need to be careful to do it properly. More skill required than you would think at first glance. I can only sand for a while each session as my hands an elbows can only take so much. It's not so bad if you are outside on a sunny day.
Tuesday, July 10, 2012
Best seat at the Movie
I arrived early and had to wait a while until the movie started. The velomobile was a big hit with the kids.
Testing the system and waiting for it to get dark. I took a picture in the dark but it didn't turn out very well. The carbon top just disappears in the dark.
We had the chance to go see a movie at the Blenkin Park next to the community centre on Quadra Island. I ended up with the best seat in the park. Being inside the velomobile was quite an advantage as it cooled off after dark. Folks sitting in chairs were wrapped up in blankets and wore toques ontheir heads. I was OK with just a sweater on and my jacket draped over me. I actually nodded off for a few minutes so I couldn't have been too cold. I would not recommend sleeping in the velomobile but it is possible in a pinch.
The screen is an inflated structure about three stories tall. It only takes a few hours to setup. The Coastal Cummunity Credit Union is the main sponsor for the event. Luckily the weather co-operated --the week before it had been raining and a few degrees colder.
The ride home was interesting as my lights failed to function properly. I had forgotten to plug a battery into the E-werk and it doesn't work properly without it. I have a Son dynamo which normally charges a battery and then runs the lights. I had tested to be sure I had lights before I left as I had charged a battery and turned them on. The lights would come on and then turn themselves off after about five seconds. Luckily it was clear night and the moon was just rising. I did have the flashing rear taillight working so cars could see me from behind. In the last half on the ride no cars passed me and I could smell the honeysuckle that is in bloom all over the island. One does go rather slowly downhill when you can't see too well. Some spots where the forest was tight on both sides of the road were pretty dark. A mini adventure not to be repeated.
Saturday, June 30, 2012
Rear Fender Etc
The three moulds for the shell lined up on the grass. The top mould is to the left and the two bottom moulds on the right. I have started sanding the right most mould as I used PVA as a release agent and it leaves some pattern in the mould. Using PVA insures that you do get a release. I was not willing to rely just on wax for a release after touching up a few spots on the plug. One more sanding in the mould gives me another chance at making it perfect. I have built quite a few moulds but have yet to get one that is absolutely perfect. This mould so far is looking very nice.
The rear fender moulds are now laminated and waiting to be trimmed. I modified the recess for the chain a bit so it is possible to use just one idler if one chooses to do so. I also added a couple of ribs to the fender so I can hoepfully build it a bit lighter as they will add considerable stiffness to the flat panel. If necessary I can turn these recesses into tubes by filling them with foam and then laminating some material over them on the inside side of the fender. The other option would be to just bond a flat sheet over the recess omitting the foam. I'll try it without either of these steps to see if it will be stiff enough.
Tuesday, June 19, 2012
Progress Report
So far I have managed to build the second mould for the Milan GT shell.
This part has been popped off the plug to clean up the parting line. If all goes well the third and final mould for the shell will be hand laid up this week. Just from looking at this mould it looks like I can avoid using peel ply in most of the two bottom parts of the shell so we will have a nice smooth finish on the inside of the parts like we do in the hulls of our kayaks. It makes them easy to keep clean as the inside surface is as smooth as the nylon film used to bag the part.
It has been a while since I did this much hand laminating. I can't see how folks do this on a regular basis. I just detest it, having to wear a respirator, gloves, coveralls and deal with sticky gooey smelly resin. I would much rather spend a bit more time and have it all enclosed under a bag. Unfortunately for making moulds hand laminating is the most reasonable way to do it.
After this there are still some more moulds to make before we can build the first Milan GT. I may take just as long to make these smaller moulds as they almost all need to be made in two or three parts so I can vacuum bag or infuse them. Some of them took serious contemplation to figure out the best way to make the moulds. The good part about these parts is most of the moulds are small and much easier to deal with as hand laminates.
This part has been popped off the plug to clean up the parting line. If all goes well the third and final mould for the shell will be hand laid up this week. Just from looking at this mould it looks like I can avoid using peel ply in most of the two bottom parts of the shell so we will have a nice smooth finish on the inside of the parts like we do in the hulls of our kayaks. It makes them easy to keep clean as the inside surface is as smooth as the nylon film used to bag the part.
It has been a while since I did this much hand laminating. I can't see how folks do this on a regular basis. I just detest it, having to wear a respirator, gloves, coveralls and deal with sticky gooey smelly resin. I would much rather spend a bit more time and have it all enclosed under a bag. Unfortunately for making moulds hand laminating is the most reasonable way to do it.
After this there are still some more moulds to make before we can build the first Milan GT. I may take just as long to make these smaller moulds as they almost all need to be made in two or three parts so I can vacuum bag or infuse them. Some of them took serious contemplation to figure out the best way to make the moulds. The good part about these parts is most of the moulds are small and much easier to deal with as hand laminates.
Friday, June 8, 2012
Progress on the Milan GT
I am almost ready to build the mould for the top of the Milan GT. It has taken a while to get to this point.
Here you can see the flange being made. You can also see the cockpit opening has been closed in so I can vacuum bag or infuse the parts. The wide flange is also necessary for this. I have also starting on some of the smaller moulds. The folks at Raderwerk send me a vey nice light carbon seat to use in the first Milan. I have been very carefull moulding the seat making sure I don't damage it.
Once the mould was made I clamped a flange on so I could make the mould wider. This is a multistep process that will take some time. I also made a mould of the back of the seat as it has two stiffening tubes built into it. My plan is to bag the front and back of the seat and then glue the part with the stiffening tubes onto the back of the seat. This with avoid having to fill the tube shapes with foam. I would be quite pleased if the weight ended up a bit less but will be happy if it ends up the same as the seat I was sent. The seat I received was less than 700 grams without any holes drilled in it.
I am almost ready to build the mould for the top of the Milan GT. It has taken a while to get to this point.
Here you can see the flange being made. You can also see the cockpit opening has been closed in so I can vacuum bag or infuse the parts. The wide flange is also necessary for this. I have also starting on some of the smaller moulds. The folks at Raderwerk send me a vey nice light carbon seat to use in the first Milan. I have been very carefull moulding the seat making sure I don't damage it.
Once the mould was made I clamped a flange on so I could make the mould wider. This is a multistep process that will take some time. I also made a mould of the back of the seat as it has two stiffening tubes built into it. My plan is to bag the front and back of the seat and then glue the part with the stiffening tubes onto the back of the seat. This with avoid having to fill the tube shapes with foam. I would be quite pleased if the weight ended up a bit less but will be happy if it ends up the same as the seat I was sent. The seat I received was less than 700 grams without any holes drilled in it.
Monday, May 28, 2012
The patterns for the Milan GT have finally arrived. Here is a picture of the shell pattern sitting outside the shop.
.
I have looked over the pattern and it is in quite good shape. There are a few spots that need touching up but nothing that will take very long. What will take longer is closing off the openings in the plug. If I am going to vaccum bag or infuse the parts I need an mould with no openings in it. In the photo below you can see a jig being made of the cutouts in the floor. I have also bonded on some drill bushings to pick up register points for mounting the rear suspension, seat and wheel wells.
Tuesday, May 15, 2012
Here is a link to a bit of video of a Milan SL. It is interesting that you can see the speedometer on the screen. The rider does hit some quite fast speeds.
I am now more determined to fit into the Milan SL than before.
First I have to build the moulds for the Milan GT. I will be going to pick up the shipment with the plugs and some parts next week. It should be arriving at the freight terminal in Vancouver tomorow or the next day. Then its just a matter of it clearing customs and I can go get it.
Monday, April 9, 2012
Milan SL & Moving
Just found an interesting picture comparing the Milan SL and the Evo K.
Now the only real question for me is will I fit. I am just a bit tall to fit at 6'2" but I am keeping my fingers crossed that my long torso and shortish legs will do the trick. I won't be completely disappointed if I don't fit as I will still have the Milan GT to ride.
Luckily is taking a little longer than expected to get the patterns(plugs) for the Milan as moving our shop and house has ended up taking longer than what I planned for. Setting up the shop properly will take lots more effort as squeezing into a space a fifth the size of before is a real challenge. When I am finally done we will have a very efficient shop that will be a pleasure to work in. Lots of nice views to the outside and all on one level. Before we had two levels and I was up and down quite a few times each day. Not that I minded the built in exercise program but it eat up some valuable time each day. Our new location is on Quadra Island just a short ferry ride away from Campbell River. As of April 20th our new phone number will be (250) 285-2154.
Thursday, March 15, 2012
Milan Velomobile coming to North America
When I first saw the Milan velomobile on the internet I thought it was rather interesting looking and liked the idea that it was a somewhat different approach to velomobile design. I wasn't sure if I could get used to the idea of the bumps and how they looked. I finally got to see one in person during ROAM and it looks much better in person than in pictures. I then had short test ride and decided that I should built it or something very similar. It has taken since then to make the right arrangements so we can build the Milan GT(formerly Milan MK2) and the Milan SL for the North American market.
The plugs for the Milan GT will arrive here in about a month. Hopefully the moulds for the Milan GT will be built before the plugs for the Milan SL arrive. The plugs for the Milan SL will leave Germany about the time I get the Milan GT plugs. We should have our first demo models done by mid summer.
The plugs for the Milan GT will arrive here in about a month. Hopefully the moulds for the Milan GT will be built before the plugs for the Milan SL arrive. The plugs for the Milan SL will leave Germany about the time I get the Milan GT plugs. We should have our first demo models done by mid summer.
Wednesday, March 14, 2012
New Signal/Running Lights
This LED light is three 2W LED's mounted on a heat sink and bonded inside the shell. It is a bit painful to look at directly from less than 20 feet. They look lots larger than the standard LED light used and are quite visible even in fun sun.
Here you can see the clear casting sticking through the shell. After bonding them to the inside of the shell I carefully sand it flush with the exterior. After sanding to 600 grit I then polish it with cutting compound. The result can be seen below.
If you look closely you can see the LEDs mounted on the white disk along with the red and black wires. Even with the somewhat involved installation procedure these lights end up being the same or less work than our previous ones. On the previous ones I had to solder 16 resistors and 16 LEDs on a board and than cast clear resin around them to create the light. After this was done you still had to cut a hole in the shell and bond them in place. The new ones are way brighter with the same energy consumption. An added bonus is you can make them fit the shape of your velo perfectly. Some hand eye co-ordination and patience required.
Subscribe to:
Posts (Atom)